-
ExxonMobil Chemical
2011–2015 гг.
CONCLUSION
During the research of ExxonMobil Chemical alcohols production in USA to export to Brazil, it is clear that they qualify to apply process costing to their production due to the nature of their production process and outcome. Since their products have final identical units and each step’s output becoming the input for the next, accumulating cost in the process, they can easily calculate the average final cost per unit dividing the whole process’ cost in a period by the final output in that period, methodology explained by Drury. It is also possible to include the logistics costs in the process, since they also accumulate during the process and one stage is needed in order to get the product to its final destination, similar to production process’ input and output model.
…
INTERNET BASED CASE STUDY – ExxonMobil Chemical Process costing is a cost keeping and measurement system largely used within the industry to assign costs where mass products are generated from raw material within a time range and consuming the same amount of labour and direct costs. It allows achieving the average unit cost by dividing all costs necessary to produce the units or the service by the total unit number produced. The objective of this analysis is to determine whether the ExxonMobil Chemical Company could apply Process Costing to assign costs to the chemical products exported to Brazil. ExxonMobil is a North America multinational open company operating in the Oil and Gas field, listed in the New York stock market, with over 100.000 employees all over the world, spread into plants, offices, refineries and logistic support, connecting the company to its customers. It has a diverse portfolio based on oil refining, from exploration to its end-use. Its structure is based on the oil extracting stages and sub-products, leading to the company that will be looked in more detail in this paper – ExxonMobil Chemicals and its chemical intermediates’ alcohols maritime exports from USA to Brazil.
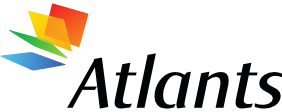